IIDEA CoBot
Der an dieser Stelle eingebundene Inhalt führt Sie auf Seiten, die von der von Google betriebenen Seite YouTube - YouTube, LLC, 901 Cherry Ave., San Bruno, CA 94066, USA - zur Verfügung gestellt werden. Mit dem Aufruf des Inhalts kann YouTube Ihre IP-Adresse und die Sprache des Systems, sowie verschiedene browserspezifische Angaben ermitteln. Wenn Sie in Ihrem YouTube-Account eingeloggt sind, ermöglichen Sie YouTube, Ihr Surfverhalten direkt Ihrem persönlichen Profil zuzuordnen. Dies können Sie verhindern, indem Sie sich aus Ihrem YouTube-Account ausloggen. YouTube verwendet Cookies und Tracking-Tools. Die Datenverarbeitungsvorgänge sowie die Zwecke der Verarbeitung können direkt bei YouTube erfragt und eingesehen werden.
In this video, Prof. Mathias Hüsing of the Institute of Mechanism Theory, Machine Dynamics and Robotics at RWTH Aachen University explains simple teaching options for collaborative robots, or CoBots for short, to support disabled and limited persons at work in the context of human-robot collaboration.
Robotics enables inclusion.
More Information about the IIDEA Project can be found at the project website
Successful completion of our DFG project: Multidirectional additive manufacturing with the plasma welding process
We are pleased to announce that we have successfully completed our DFG-funded project in cooperation with the Institute of Welding and Joining Technology RWTH Aachen University on multidirectional additive manufacturing with the plasma welding process!
Highlights of the project:
– Process control through unified process monitoring and control in ROS: Thanks to the use of the Robot Operating System (ROS), we were able to realize high-precision process monitoring and control. This ensures optimum process reliability and repeat accuracy.
– Multidirectional trajectory planning: By developing and implementing our path and trajectory planning, we have succeeded in enabling complex welding movements for production. This increases the flexibility and variety of possible applications within additive manufacturing.
– Stable deposition possible even on inclines thanks to workpiece handling: Our solution for workpiece handling makes it possible to achieve stable layer deposition even on inclined surfaces. This expands the areas of application and significantly improves the quality of the manufactured parts.
A big thank you to the entire team for the outstanding collaboration and to the German Research Foundation (DFG) for supporting this groundbreaking project. We are looking forward to the future developments and applications of our research results in industry!
You can find the list of our publications here.
Contact person:
Markus Schmitz
Jan Wiartalla
IIDEA at the BIH Working Committee of the Technical Advisory Services in Dortmund
An exciting day at the BIH Working Committee of the Technical Advisory Services in Dortmund!
We had the great opportunity to present our project to the integration and inclusion offices from all of Germany’s federal states.
Prof. Hüsing gave an exciting presentation on the opportunities offered by collaborative robotics in the context of inclusion.
He also presented the IIDEA project, which now provides technical advisory services with the support they need to educate companies about collaborative robotics. We support this with the IIDEA Infomobile and hands-on procedures).
In addition, Carlo was able to offer the participants an insight into the programming of collaborative robots in order to give them a deeper understanding of the possible applications and their implementation.
It was interesting to meet the department heads of the technical advisory services from 16 federal states in person. Almost all federal states were represented – proof of the interest and relevance of the topic. A big thank you to all participants for their commitment and enthusiasm for the future of inclusive robotics!
contact person:
Mathias Hüsing
Carlo Weidemann
Elodie Hüsing
Sophie-Charlotte Keunecke
Christina Jansen
Semi-Automated Tile-Laying Aid
Der an dieser Stelle eingebundene Inhalt führt Sie auf Seiten, die von der von Google betriebenen Seite YouTube - YouTube, LLC, 901 Cherry Ave., San Bruno, CA 94066, USA - zur Verfügung gestellt werden. Mit dem Aufruf des Inhalts kann YouTube Ihre IP-Adresse und die Sprache des Systems, sowie verschiedene browserspezifische Angaben ermitteln. Wenn Sie in Ihrem YouTube-Account eingeloggt sind, ermöglichen Sie YouTube, Ihr Surfverhalten direkt Ihrem persönlichen Profil zuzuordnen. Dies können Sie verhindern, indem Sie sich aus Ihrem YouTube-Account ausloggen. YouTube verwendet Cookies und Tracking-Tools. Die Datenverarbeitungsvorgänge sowie die Zwecke der Verarbeitung können direkt bei YouTube erfragt und eingesehen werden.
As part of the ErgoFli project, an innovative system is being developed in collaboration with project partners to help tile layers make their work more ergonomic and efficient.
In the video you can see how the system works in the Gazebo simulation environment. The robot automatically removes tiles from a magazine and matches them perfectly to the tiles already laid. With automatic processes, several tiles can be laid in succession to optimize the work process.
Our aim is to create a tool that not only reduces the workload for tilers, but also improves their working environment. We are excited about the progress and look forward to sharing more insights with you soon!
Find out more about the project here.
Contact person:
Mark Witte
Jan Wiartalla
IMBA training for the IIDEA project team
Our IIDEA-project team took part in a training course on the “Integration of people with disabilities into the world of work” (IMBA).
IMBA is positioned at the interface of medical and occupational rehabilitation and enables a precise description and comparison of work requirements and human abilities. The training covered the basics of IMBA, with a particular focus on the defined characteristics that serve as the basis for the assessment of work requirements and abilities. A highlight of the training was the introduction to the “Marie Plus” software, which is closely linked to the IMBA concept. The training was conducted by Torsten Alles, Ph.D., Managing Director of iqpr. His extensive knowledge and experience helped to emphasize the importance of IMBA in occupational therapy and activity-based medical rehabilitation.
We are convinced that this training will support our previous research and make a valuable contribution to the IIDEA project. We are grateful for the expertise we have gained through this training and look forward to applying the acquired knowledge in our daily work.
contact person:
Mathias Hüsing
Carlo Weidemann
Elodie Hüsing
Sophie-Charlotte Keunecke
Christina Jansen
Rapid Prototyping in the development of robot hardware
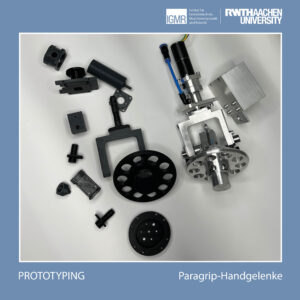
As part of the RobWeld project, new wrists and gripping mechanisms were developed for the PARAGRIP developed and built at IGMR.Through iterative design processes using rapid prototyping in 3D printing, we have perfected functionalities, ease of assembly and the manufacturability of components. The result? An elaborate design that combines steel and aluminum components.In the next step, the design can now be extensively tested before it is used on the robot.
You can find more information about the RobWeld project here.
Contact person:
Jan Wiartalla