Kategorie: ‘Allgemein’
May 8th, 2024 | by
Jansen, Christina

An exciting day at the BIH Working Committee of the Technical Advisory Services in Dortmund!
We had the great opportunity to present our project to the integration and inclusion offices from all of Germany’s federal states.
Prof. Hüsing gave an exciting presentation on the opportunities offered by collaborative robotics in the context of inclusion.
He also presented the IIDEA project, which now provides technical advisory services with the support they need to educate companies about collaborative robotics. We support this with the IIDEA Infomobile and hands-on procedures).
In addition, Carlo was able to offer the participants an insight into the programming of collaborative robots in order to give them a deeper understanding of the possible applications and their implementation.
It was interesting to meet the department heads of the technical advisory services from 16 federal states in person. Almost all federal states were represented – proof of the interest and relevance of the topic. A big thank you to all participants for their commitment and enthusiasm for the future of inclusive robotics!
contact person:
Mathias Hüsing
Carlo Weidemann
Elodie Hüsing
Sophie-Charlotte Keunecke
Christina Jansen
Kategorie: Allgemein
No Comments »
May 7th, 2024 | by
Jansen, Christina
https://youtu.be/2aJtSazLz1M
As part of the ErgoFli project, an innovative system is being developed in collaboration with project partners to help tile layers make their work more ergonomic and efficient.
In the video you can see how the system works in the Gazebo simulation environment. The robot automatically removes tiles from a magazine and matches them perfectly to the tiles already laid. With automatic processes, several tiles can be laid in succession to optimize the work process.
Our aim is to create a tool that not only reduces the workload for tilers, but also improves their working environment. We are excited about the progress and look forward to sharing more insights with you soon!
Find out more about the project here.
Contact person:
Mark Witte
Jan Wiartalla
Kategorie: Allgemein, C++, Digital Shadow, Entwicklung und Konstruktion, Lokalisierung, Mobile Robotics, Mobile Robotik, Planung, Prototypenbau, Python, Roboterprogrammierung, ROS, Simulationen, SPS, Virtuelle Inbetriebnahme, Zukunft der Arbeit
No Comments »
May 7th, 2024 | by
Jansen, Christina
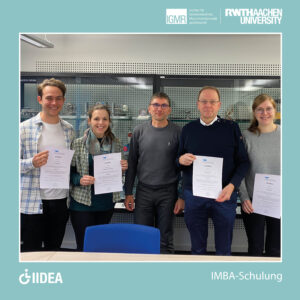
Our IIDEA-project team took part in a training course on the “Integration of people with disabilities into the world of work” (IMBA).
IMBA is positioned at the interface of medical and occupational rehabilitation and enables a precise description and comparison of work requirements and human abilities. The training covered the basics of IMBA, with a particular focus on the defined characteristics that serve as the basis for the assessment of work requirements and abilities. A highlight of the training was the introduction to the “Marie Plus” software, which is closely linked to the IMBA concept. The training was conducted by Torsten Alles, Ph.D., Managing Director of iqpr. His extensive knowledge and experience helped to emphasize the importance of IMBA in occupational therapy and activity-based medical rehabilitation.
We are convinced that this training will support our previous research and make a valuable contribution to the IIDEA project. We are grateful for the expertise we have gained through this training and look forward to applying the acquired knowledge in our daily work.
Here you can find more information about the IIDEA project.
contact person:
Mathias Hüsing
Carlo Weidemann
Elodie Hüsing
Sophie-Charlotte Keunecke
Christina Jansen
Kategorie: Allgemein, Aufgabenplanung, C++, Data Lake, IGMR, Industrie 4.0, Inklusion, inklusive Arbeit, Inklusive Arbeitsplätze, MDAM, Mensch-Maschine-Kollaboration, Mensch-Roboter-Kollaboration, Mobile Robotics, Mobile Robotik, Planung, Prototypenbau, Regelung, Roboter, Trajektorie
No Comments »
April 29th, 2024 | by
Jansen, Christina
As part of the RobWeld project, new wrists and gripping mechanisms were developed for the PARAGRIP developed and built at IGMR.Through iterative design processes using rapid prototyping in 3D printing, we have perfected functionalities, ease of assembly and the manufacturability of components. The result? An elaborate design that combines steel and aluminum components.In the next step, the design can now be extensively tested before it is used on the robot.
You can find more information about the RobWeld project here.
Contact person:
Jan Wiartalla
Kategorie: Allgemein, Entwicklung, Entwicklung und Konstruktion, Greiferentwicklung, Prototypen, Prototypenbau
No Comments »
April 22nd, 2024 | by
Jansen, Christina
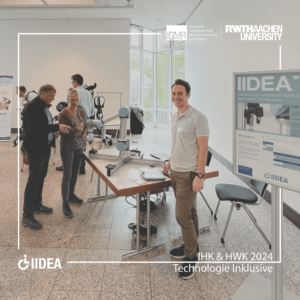
A successful day for the IIDEA project at the IHK and HWK event “Technology included – exoskeletons & co. – aids for everyday working life”! Prof. Hüsing and our project manager Carlo represented the IIDEA project at the event in Düsseldorf. Prof. Hüsing gave an exciting presentation on “Inclusive working environment through collaborative robotics: opportunities and perspectives for your company.” At the stand in the foyer, we were also able to inspire many organizations and companies for our project. We look forward to visiting them soon and working together on inclusive working environments!
Here you can find more information about the event in Düsseldorf.
contact:
Prof. Mathias Hüsing
Carlo Weidemann
Kategorie: Allgemein
No Comments »
April 10th, 2024 | by
Jansen, Christina
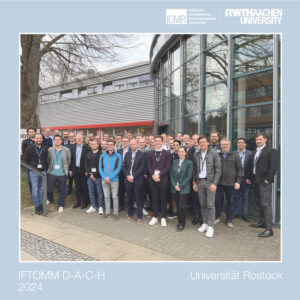
The IGMR was represented at this year’s IFToMM DACH in Rostock with a wide range of topics!
We presented exciting insights into the following topics:
– Extension of the PlanSys2 framework
– Digital twins in intelligent manufacturing
– Function-driven multidirectional additive manufacturing
– Energy-efficient non-uniformly translating gerars
– Digital teaching offerings in machine dynamics
Curious? The conference proceedings including our contributions are available here!
Contact person:
Simon Schläger
Sophie Charlotte Keunecke
Mark Witte
Thomas Knobloch
Nils Brückmann
A big thank you to the organizers and all participants for a great conference with inspiring exchange!
Kategorie: Allgemein, IGMR, Industrie 4.0
No Comments »
December 18th, 2023 | by
Jansen, Christina
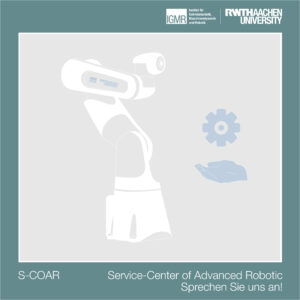
Our expertise extends to the seamless integration of robots into test benches, the optimization of showcases with existing robots and the adaptation of measurements and sensor technology for an automated solution using robots.
Robots are playing an increasingly important role in a wide range of research projects. However, there is often a lack of expertise and time to use them effectively and in a user–friendly way – and this is exactly where we come in!
Our services include:
– The integration of robots into your test benches
– The further use of existing robots for showcases
– The adaptation of measurements and sensors using robot technology
– Troubleshooting for robots
– Planning and implementation of research projects with the use of robots
– Ideas and support for automation in various specialist areas
Dr. Markus Schmitz is your contact for the implementation and planning of automation projects and for technical advice. Please send requests for quotations to scoar@igmr.rwth-aachen.de.
Kategorie: Allgemein, Roboter, Robotik
No Comments »
October 18th, 2023 | by
Berna Soysal
Transferring observations into a planning language: An automated approach in the field of cooking
In the Robot Cooking project, an automated method is developed to analyze and identify motion data and convert it into a machine-readable planning language. This is done using a cooking scenario as an example in which the motion data is captured by recording the hand pose of the cook.
The recording is done using a motion capture system consisting of seven cameras and a glove with three markers on the back of the chef’s hand. The position of the markers is determined by triangulation. This provides enough information to derive the hand pose. The recording is done at 120 frames per second. Before the cooking process, all objects in the workspace are identified and their initial positions determined. Motion data is continuously recorded and converted into poses with time stamps. Additional information such as velocity, acceleration and angle in relation to the tabletop are derived from the raw data.
A initial structure of the dataset is created by finding the side actions using classification. Here, pick, move and place are identified as recurrent side actions. A separate training dataset is used to train a classifier that recognizes these actions. This enables an easier analysis of the remaining actions.
Clustering is applied to identify unknown actions. A dynamic approach allows analysis despite high variability in execution. A unique fingerprint for each action is found, based on the orientation of the back of the hand and its speed on the table plane, to assign each frame to a cluster and finally to an action.
The knowledge gained from classification and clustering is translated into a machine-readable Planning Domain Definition Language (PDDL). A schedule is created, with known actions directly assigned. Start and end positions are specified, and virtual object tracking is used to represent the progression of objects during cooking. For unknown actions, preconditions and effects are handled dynamically. The results are translated into a machine-readable PDDL. This formal representation enables efficient automatic scheduling and execution of the previously demonstrated cooking task.
Additional information is available in the video linked above, the poster and the paper.
Contact:
Markus Schmitz
Kategorie: Allgemein
No Comments »
July 6th, 2023 | by
Jansen, Christina
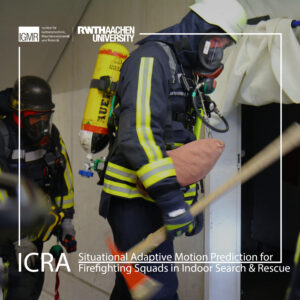
We presented our paper “Situational Adaptive Motion Prediction for Firefighting Squads in Indoor Search and Rescue” at ICRA in the Long-Term Human Motion Prediction workshop.
Firefighting is a complex but poorly automated task. To minimize ergonomic and safety risks for firefighters, robots could be used in a collaborative approach. To enable human-robot teams in firefighting, important fundamentals are still missing. Among other things, the robot must predict human movement because occlusions are ubiquitous. In this work, we propose a novel motion prediction method for firefighting squads in indoor attack. Squad paths are generated using an optimal graph-based planning approach that represents firefighter tactics. Paths are generated on a per-room basis, allowing dynamic local adaptation of paths without global replanning. The movement of individual agents is simulated using a modification of the Headed Social Force Model. We evaluate the feasibility of the pipeline using a novel dataset generated from real footage and show its computational efficiency.
Contact: Elodie Hüsing
Kategorie: Allgemein
No Comments »
June 2nd, 2023 | by
Jansen, Christina
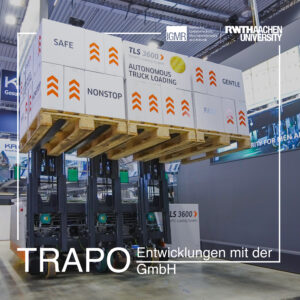
The IGMR – RWTH Aachen supports Trapo GmbH in the further development and integration of trajectory planning and trajectory execution algorithms for the new Trapo Loading System robot. Compared to the old TLS, the navigation of the new TLS is realized with the MoveBase Framework of the Robot Operating System (ROS). For this purpose, together with Trapo GmbH, we have created a special configuration for car-like structure for the local MoveBase Planner. The new TLS was last presented at the LogiMat trade fair.
Contact:
Daniel Gossen
Kategorie: Allgemein, ROS, Trapo AG
No Comments »