November 28th, 2024 | by
Jansen, Christina

Prof. Hüsing gave a presentation on “Efficient Kinematics Development for Door and Closure Systems”. In addition, the 160 conference participants were able to see for themselves the efficient design of motion devices using the “Mechanism Developer” (MechDev) program.
To thank Prof. Hüsing for his presentation, a tree was planted on behalf of the conference organizer Automotive Circle.
contact:
Mathias Hüsing
Kategorie: Allgemein, Bewegungsplanung
Keine Kommentare »
November 21st, 2024 | by
Jansen, Christina
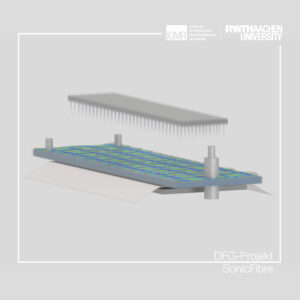
As part of our joint project at the Institute of Applied Mechanics (IAM) and @Institute of Textile Technology (ITA), we are working on an exciting development: the production of nonwovens with optimized efficiency.
The challenge: During needling, a central process step, the fibers are entangled by mechanical movement in order to produce a stable nonwoven from a loose fiber bundle. This creates high frictional forces – a problem that leads to wear on the machine parts.
Our solution: We optimize the friction between the fibres through the targeted excitation of high-frequency vibrations in the ultrasonic range. Our focus is on stimulating a perforated plate in the ultrasonic range in such a way that a suitable vibration pattern is generated – and thus making the process more efficient and gentle.
You can find more information about the project here.
contact:
Johanens Bolk
Kategorie: Industrie, Industrie 4.0, Zukunft der Arbeit
Keine Kommentare »
November 7th, 2024 | by
Jansen, Christina
Fully automatic disassembly with precision!
Our new robotic system is revolutionizing the disassembly of electric car batteries. Using the Neura Lara 8 robot and the latest image processing technologies, we recognize screws fully automatically and position the robot precisely to remove them safely.
Thanks to the integration of YOLOv8 and Intel RealSense depth cameras, the system can locate screws in real time and position them optimally on its own. No manual intervention necessary – the system works completely autonomously!
Our goal: to make the recycling process safer, faster and more efficient. Fewer risks for workers and maximizing the recovery of raw materials at the same time. This is the future of the circular economy!
You can find more information about #dimonta here.
contact:
Markus Schmitz
Daniel Gossen
Kategorie: AI Task Planning, Algorithmen, Automated Task Planning, dimonta, Industrial Robotics, Industrial Scenario, Industrie, Industrie 4.0, industrielle Robotik, KI, KI Aufgabenplanung, KI Objekterkennung, künstliche Intelligenz, Objekterkennung, Roboter, Roboterprogrammierung, Robotic Systems, Robotik, ROS, Sensor
Keine Kommentare »
October 31st, 2024 | by
Jansen, Christina
At the ASME IDETC-CIE conference in Washington, DC, we had the opportunity to present the prototype of the “3D Capsule Compliant Gripper”. This novel surgical manipulation tool was specifically designed to make lymph node isolation even more precise and gentle.
Our approach: a capsule-like structure with flexible, shape-optimized elements that have been tailored using a hill-climbing mutation algorithm. The white “petals” of the prototype were 3D printed from PLA, the red flexible components from TPU. Thanks to the cost-effective production at our institute, we were able to create the first efficient solution on a macro scale, which serves as a proof of concept.
Contact: Estefania Hermoza Llanos
Kategorie: IGMR, Industrie 4.0, industrielle Robotik, Roboter, Roboter unterstützter Patiententransport, Roboterprogrammierung, Robotik
Keine Kommentare »
October 1st, 2024 | by
Ruland, Stefan Wolfgang
Der an dieser Stelle eingebundene Inhalt führt Sie auf Seiten, die von der von Google betriebenen Seite YouTube - YouTube, LLC, 901 Cherry Ave., San Bruno, CA 94066, USA - zur Verfügung gestellt werden. Mit dem Aufruf des Inhalts kann YouTube Ihre IP-Adresse und die Sprache des Systems, sowie verschiedene browserspezifische Angaben ermitteln. Wenn Sie in Ihrem YouTube-Account eingeloggt sind, ermöglichen Sie YouTube, Ihr Surfverhalten direkt Ihrem persönlichen Profil zuzuordnen. Dies können Sie verhindern, indem Sie sich aus Ihrem YouTube-Account ausloggen. YouTube verwendet Cookies und Tracking-Tools. Die Datenverarbeitungsvorgänge sowie die Zwecke der Verarbeitung können direkt bei YouTube erfragt und eingesehen werden.
In this video, Prof. Mathias Hüsing of the Institute of Mechanism Theory, Machine Dynamics and Robotics at RWTH Aachen University explains simple teaching options for collaborative robots, or CoBots for short, to support disabled and limited persons at work in the context of human-robot collaboration.
Robotics enables inclusion.
More Information about the IIDEA Project can be found at the project website
https://www.iidea.rwth-aachen.de/cms/~badhmp/iidea/?lidx=1
Kategorie: Cobot, IGMR, Industrie, Inklusion, inklusive Arbeit, Inklusive Arbeitsplätze, Kollaboration, kollaborierenden Roboter, Mensch-Maschine-Kollaboration, Mensch-Roboter-Kollaboration, Roboter
Keine Kommentare »
August 20th, 2024 | by
Jansen, Christina
We are pleased to announce that we have successfully completed our DFG-funded project in cooperation with the Institute of Welding and Joining Technology RWTH Aachen University on multidirectional additive manufacturing with the plasma welding process!
Highlights of the project:
– Process control through unified process monitoring and control in ROS: Thanks to the use of the Robot Operating System (ROS), we were able to realize high-precision process monitoring and control. This ensures optimum process reliability and repeat accuracy.
– Multidirectional trajectory planning: By developing and implementing our path and trajectory planning, we have succeeded in enabling complex welding movements for production. This increases the flexibility and variety of possible applications within additive manufacturing.
– Stable deposition possible even on inclines thanks to workpiece handling: Our solution for workpiece handling makes it possible to achieve stable layer deposition even on inclined surfaces. This expands the areas of application and significantly improves the quality of the manufactured parts.
A big thank you to the entire team for the outstanding collaboration and to the German Research Foundation (DFG) for supporting this groundbreaking project. We are looking forward to the future developments and applications of our research results in industry!
You can find the list of our publications here.
Contact person:
Markus Schmitz
Jan Wiartalla
Kategorie: Allgemein
Keine Kommentare »