Kategorie: ‘IGMR’
March 4th, 2025 | by
Jansen, Christina

We kicked-off our new project “AuBa@C – Automation of Battery Disassembly using Advanced Hardware and Software for Battery Recycling” together with cylib. Here at IGMR, we conduct research into automated disassembly using robots. In the project together with cylib, we can transfer our expertise from projects such as Bots2ReC, SHEREC or di.monta to the disassembly of EV batteries.
We are excited to collaborate with cylib (Dr. Stefan-Octavian Bezrucav (Head of Pre-Processing and Robotics Expert) and Sara Ognjanovic (Project Manager for Automation in Battery Discharge and Disassembly).)
This project is supported by the “KUER.NRW | Grüne Gründungen Nordrhein-Westfalen” funding initiative, under the framework of the European Regional Development Fund (EFRE/JTF NRW 2021-2027), coordinated by the Ministry for the Environment, Nature Conservation, and Transport of North Rhine-Westphalia and the Projektträger Jülich (PtJ).
contact:
Stefan Groß
Kategorie: dimonta, IGMR, Roboter
No Comments »
October 31st, 2024 | by
Jansen, Christina
At the ASME IDETC-CIE conference in Washington, DC, we had the opportunity to present the prototype of the “3D Capsule Compliant Gripper”. This novel surgical manipulation tool was specifically designed to make lymph node isolation even more precise and gentle.
Our approach: a capsule-like structure with flexible, shape-optimized elements that have been tailored using a hill-climbing mutation algorithm. The white “petals” of the prototype were 3D printed from PLA, the red flexible components from TPU. Thanks to the cost-effective production at our institute, we were able to create the first efficient solution on a macro scale, which serves as a proof of concept.
Contact: Estefania Hermoza Llanos
Kategorie: IGMR, Industrie 4.0, industrielle Robotik, Roboter, Roboter unterstützter Patiententransport, Roboterprogrammierung, Robotik
No Comments »
October 1st, 2024 | by
Ruland, Stefan Wolfgang
Der an dieser Stelle eingebundene Inhalt führt Sie auf Seiten, die von der von Google betriebenen Seite YouTube - YouTube, LLC, 901 Cherry Ave., San Bruno, CA 94066, USA - zur Verfügung gestellt werden. Mit dem Aufruf des Inhalts kann YouTube Ihre IP-Adresse und die Sprache des Systems, sowie verschiedene browserspezifische Angaben ermitteln. Wenn Sie in Ihrem YouTube-Account eingeloggt sind, ermöglichen Sie YouTube, Ihr Surfverhalten direkt Ihrem persönlichen Profil zuzuordnen. Dies können Sie verhindern, indem Sie sich aus Ihrem YouTube-Account ausloggen. YouTube verwendet Cookies und Tracking-Tools. Die Datenverarbeitungsvorgänge sowie die Zwecke der Verarbeitung können direkt bei YouTube erfragt und eingesehen werden.
In this video, Prof. Mathias Hüsing of the Institute of Mechanism Theory, Machine Dynamics and Robotics at RWTH Aachen University explains simple teaching options for collaborative robots, or CoBots for short, to support disabled and limited persons at work in the context of human-robot collaboration.
Robotics enables inclusion.
More Information about the IIDEA Project can be found at the project website
https://www.iidea.rwth-aachen.de/cms/~badhmp/iidea/?lidx=1
Kategorie: Cobot, IGMR, Industrie, Inklusion, inklusive Arbeit, Inklusive Arbeitsplätze, Kollaboration, kollaborierenden Roboter, Mensch-Maschine-Kollaboration, Mensch-Roboter-Kollaboration, Roboter
No Comments »
May 7th, 2024 | by
Jansen, Christina
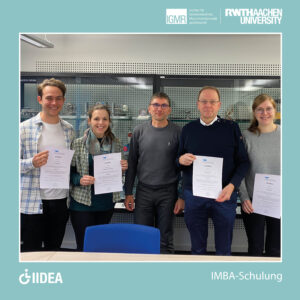
Our IIDEA-project team took part in a training course on the “Integration of people with disabilities into the world of work” (IMBA).
IMBA is positioned at the interface of medical and occupational rehabilitation and enables a precise description and comparison of work requirements and human abilities. The training covered the basics of IMBA, with a particular focus on the defined characteristics that serve as the basis for the assessment of work requirements and abilities. A highlight of the training was the introduction to the “Marie Plus” software, which is closely linked to the IMBA concept. The training was conducted by Torsten Alles, Ph.D., Managing Director of iqpr. His extensive knowledge and experience helped to emphasize the importance of IMBA in occupational therapy and activity-based medical rehabilitation.
We are convinced that this training will support our previous research and make a valuable contribution to the IIDEA project. We are grateful for the expertise we have gained through this training and look forward to applying the acquired knowledge in our daily work.
Here you can find more information about the IIDEA project.
contact person:
Mathias Hüsing
Carlo Weidemann
Elodie Hüsing
Sophie-Charlotte Keunecke
Christina Jansen
Kategorie: Allgemein, Aufgabenplanung, C++, Data Lake, IGMR, Industrie 4.0, Inklusion, inklusive Arbeit, Inklusive Arbeitsplätze, MDAM, Mensch-Maschine-Kollaboration, Mensch-Roboter-Kollaboration, Mobile Robotics, Mobile Robotik, Planung, Prototypenbau, Regelung, Roboter, Trajektorie
No Comments »
April 10th, 2024 | by
Jansen, Christina
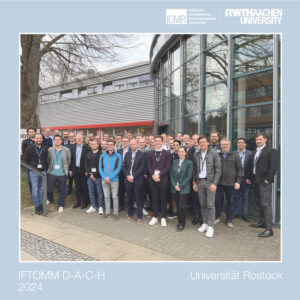
The IGMR was represented at this year’s IFToMM DACH in Rostock with a wide range of topics!
We presented exciting insights into the following topics:
– Extension of the PlanSys2 framework
– Digital twins in intelligent manufacturing
– Function-driven multidirectional additive manufacturing
– Energy-efficient non-uniformly translating gerars
– Digital teaching offerings in machine dynamics
Curious? The conference proceedings including our contributions are available here!
Contact person:
Simon Schläger
Sophie Charlotte Keunecke
Mark Witte
Thomas Knobloch
Nils Brückmann
A big thank you to the organizers and all participants for a great conference with inspiring exchange!
Kategorie: Allgemein, IGMR, Industrie 4.0
No Comments »
April 24th, 2023 | by
Jansen, Christina
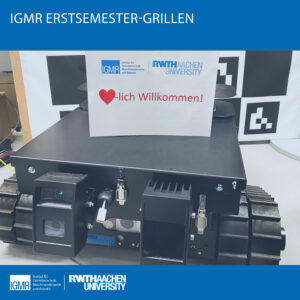
The Institute of Transmission Technology, Machine Dynamics and Robotics welcomes all new first-semester Master’s students!
The summer semester started on 03.04.2023 and with it the Master’s program for many first-semester students. At a welcome barbecue organized by the Mechanical Engineering student council, we were able to introduce our institute and talk to students.
Sophie Charlotte Keunecke, Nils Brückmann, Vincent Brünjes and Thomas Knobloch welcomed the new Master’s students from the Faculty of Mechanical Engineering at the IGMR. This allowed the students to make their first contacts with the institutes and also get to know various projects. A special highlight was the presentation of the Robot Companion by Maximilian Hilger!
We would like to thank the Mechanical Engineering student council for this great offer and your immense commitment.
We wish all new first-year students all the best for their studies and an unforgettable time at RWTH and the Faculty of Mechanical Engineering.
Contacts:
Sophie-Charlotte Keunecke
Nils Brückmann
Vincent Brünjes
Thomas Knobloch
Kategorie: IGMR, Lehre, Masterarbeit, Rettungsrobotik, Robot Companion
No Comments »
February 22nd, 2023 | by
Jansen, Christina
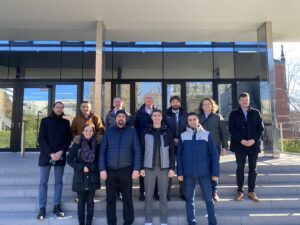
After a long corona break, the IGMR was delighted to welcome a delegation from the Technical University of Liberec (TUL) to the institute.
Four different institutes of the Technical University of Liberec introduced us to their fascinating projects and interesting presentations before we worked out common research interests in smaller workshops.
The Technical University of Liberec and the IGMR can already look back on many years of joint exchange and close cooperation; the restrictions imposed by the pandemic have not weakened this, but have severely limited it.
Therefore we are pleased to be able to strengthen our cooperation with new, joint research interests in the future.
Contact: Sophie Charlotte Keunecke
Kategorie: IGMR
No Comments »
April 8th, 2022 | by
Jansen, Christina
In a joint research project of the IGMR together with the ISF of the RWTH Aachen University, the Multidirectional Additive Manufacturing (MDAM) of metallic components is being researched. In order to optimize the multi-armed. Paragrip robot for this application, student Raphael Hoffmann has developed an innovative concept of a new robotic wrist in his bachelor thesis. The concept enables the welding current to be conducted directly through the wristsm without the need for an additional ground cable attached to the print bed. Moreover, the wrists enable form fitting gripping of the print bed with self-centering to minimize positioning inaccuracies.
You can find the video on our YouTube channel: https://youtu.be/VdT1rjYG4D0
Contact:
Jan Wiartalla
Kategorie: IGMR, Industrie 4.0, Kollaboration, Lokalisierung, MRK, Planung, Simulationen, Synthese
No Comments »
April 5th, 2022 | by
Jansen, Christina
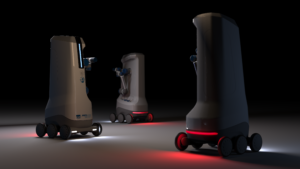
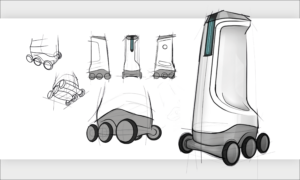
MobiLamas is a concept for free-float charging in the city of the future. In our vision, individual transport will shift from cars to public transport, complemented by so-called last-mile vehicles (e.g., electric bikes or scooters). In such environments, ecological and economical solutions are needed to enable safe and smart charging for a variety of devices. MobiLamas are intelligent mobile robots that interact with last-mile vehicles and charging stations, and safely navigate urban spaces in the presence of pedestrians.
Contact:
Jan-Lukas Archut
Kategorie: IGMR, künstliche Intelligenz, Mobile Manipulation, Virtuelle Prototypen
No Comments »